The thermal resistance junction to case is an important parameter for the reliability of the electronics devices such as light emitted diodes (LEDs) and power modules. Because degradation of these devices are temperature driven. LED systems can be today differentiated not only in high-power, mid-power and low-power application but also concerning reliability, i.e. high reliability and low reliability. On the one side, low-cost LED consumer goods and, unfortunately, partly also replacement LED bulbs are located at the low reliability side of the lighting applications. On the other side, reliability and long lifetime determines the economic and ecological success of high-end LED illumination systems, e.g. outdoor illumination, signalling, agricultural LED systems and automotive lighting. LED lighting systems can in general reach very long lifetime of up to 100.000 h when appropriate designed and business models are based on the failure free operation of the light sources. Junction temperature and drive current are the key parameters which determine lumen degradation. In addition to the slow lumen degradation also catastrophic failures of the LED can occur. For eliminating these failures not only die and package design but also process and material control in manufacturing is important. Finally the environmental conditions during operation like humidity, corrosive atmosphere and thermo-mechanical stress are fundamental for the lifetime of the LED systems.

Because many failures are driven by the junction temperature TJ of a LED, thermal management is essential to realize cost competitive but reliable LED systems. Transient thermal analysis (TTA) is a powerful approach to measure the junction temperature of the LEDs in a system and the thermal resistance Rth_el of the LED module and is standardized in the MIL-STD-750F (3100 Series).
1. Automatic panel level transient thermal tester
TTA is presently still work- and time-consuming and not automated. This center has developed an automatic panel level TTA tester. The tester targets to ease TTA during reliability assessment and for production inspection. The LED panel is placed on the temperature stabilized table of a xyz-system.
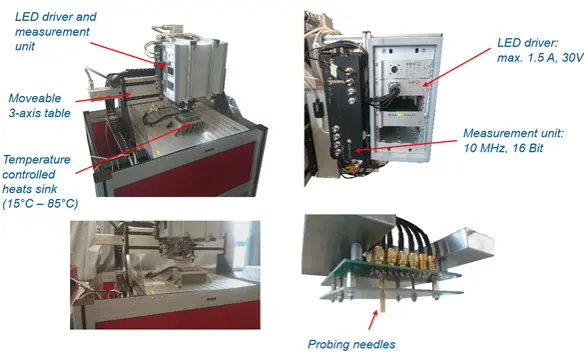
The position of the electrical test pads of the LEDs are read into the machine from Gerber data. The measurement electronics is mounted on the xyz-system to enable the use of short cables with low parasitic inductance. The LEDs are contacted by 4-point probes. To resolve the thermal resistance between the LED die (first level interconnect) and the substrate the forward voltage of the LEDs after current switching need to be measured as early as possible, i.e. well below 10μs. The developed current source allows very fast switching within 100ns and stabilize the detection current within less than 5μs. To evaluate the thermal path and the thermal resistance the relative thermal resistance measurement method is applied.
TTA can be applied also for reliability testing. The location of failures can be identified. For example, it is possible to distinguish between failures such as delamination of LED die or cracking of solder interconnect from the LED package to the printed circuit board (PCB).
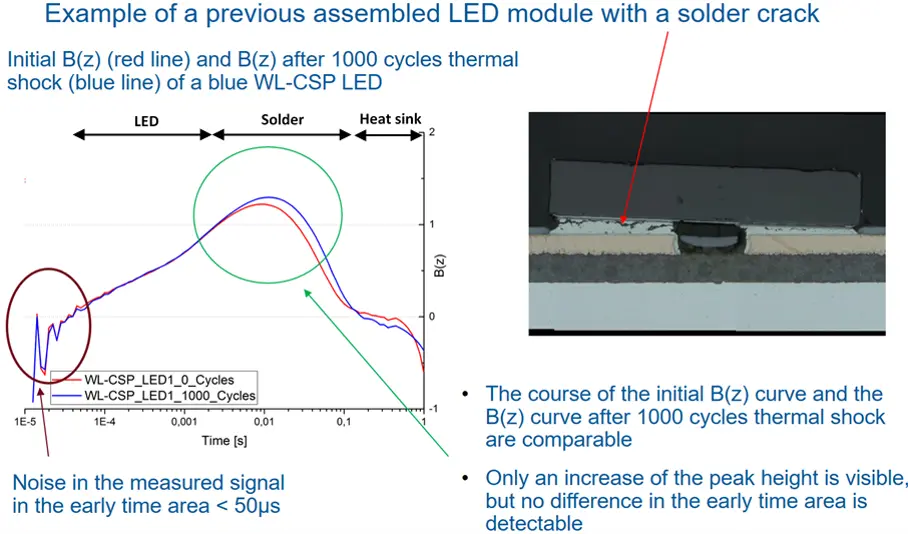
2. In-situ TTA test equipment for combined high temperature operational life (HTOL) and temperature cycle
To measure the thermal path In-Situ a new test system was build up. The LED modules are mounted on a temperature controlled heat sink which is temperature cycled between low (Tmin = -20°C), medium (TRT = +25°C) and high (Tmax = 125°C) temperature. The LEDs can be switched off during the test (passive temperature cycle test) or they are driven at nominal current (combined operational life and temperature cycle). The LEDs are connected by a multiplexer to the pulsed current source. By an additional driver and switches all LEDs can be switched on or off continuously.
In the combined operational life and temperature cycle test for a short time the LEDs are switched off and by TTA the Zth(t) is measured. Due to differences in thermo-mechanical stress under hot and cold conditions, additional information can be obtained. Target is to identify failures earlier by measuring at room temperature, Tmax and Tmin.
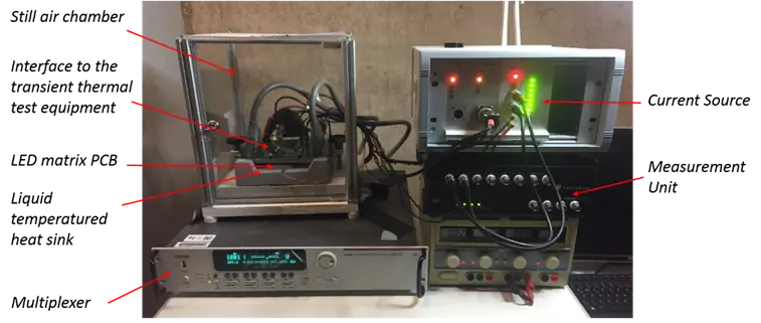
Open positions
If you are interested in vacancies for student work within the research group, please send an email with CV to assistenz-iimo-elger.de.